What to Consider When Choosing a Mask?
There are some 100 million bacteria contained in a gram of saliva or material produced by coughing/sneezing. In addition, a person performing their task without wearing special clothing emits 2 million particles per minute. As such, the biggest polluter in any cleanroom is people.
Indeed, 75 percent of cleanroom contamination comes from operators. These emissions can be reduced by 80-90 percent if appropriate protective clothing is worn along with an adapted mask, where pollutants like dust, airborne microbes, and aerosol particles are filtered to minimize the introduction, generation, and retention of particles within the room. There are a number of criteria to consider when choosing a cleanroom mask from those available on the market:
Performance
The first criteria to consider is that of performance where, with or without sterilization, we need to ensure suitable performance to protect the room environment. Performance can be measured in a number of ways:
Particle Emission
Masks with low particle emissions are preferred and this can be tested using the Helmke drum test (according to method IEST-RP-CC003.4). This test measures the number of particles released through a drum stirring the mask in all directions and is the reference test for qualifying equipment entering cleanrooms and controlled environments. For emissions, particles are stratified as ≥0.3µm and ≥0.5µm in size and the level of such emissions determines suitability for a certain grade of cleanroom.
Filtration Performance
Masks with good filtration performance should reduce the risk of human contamination. Such risk can be determined using bacterial filtration efficiency (BFE) as a measure (based on the EN 14683 2019 + AC 2019 standard), with or without sterilization. A BFE of greater than 98 percent is highly recommended. In addition, particle filtration efficiency (PFE) and virus filtration efficiency (VFE) testing should be carried out to complete the risk analysis and limit contamination, as bacteria, particles, and viruses are not the same size and have different modes of transmission.
Packaging
Packaging should encourage good dressing protocol in different cleanroom operating layouts. Indeed, double or triple packaging is recommended and, depending on whether the mask is sterilized or not, individual packaging could/should be mandatory as well.
User Comfort
The second criteria is to ensure comfort for the user in order to optimize the donning period and to limit misuse and thus contamination risk.
Fastenings
The availability of different fastenings (e.g. ties, head-loops, or ear-loops) depending upon the application and the other protective clothing available can help to optimize donning and doffing. A malleable and adjustable nose piece also ensures a good fit.
Sizing
According to the update to GMP Annex 1, a mask and goggles must cover the entire face. As facial features differ from person to person, it is thus important to have different options available to the wearer by choosing masks that are available in multiple sizes.
Breathability
Workers can stay in a cleanroom environment for several hours and as such breathability is crucial. A good level of breathability performance can be determined using ΔP values (based on the EN 14683 2019 + AC 2019 standard). A ΔP value of less than 60Pa/cm² is recommended (Figure 1). In addition, different mask shapes (e.g. duckbill masks) can provide a larger breathing chamber that aids breathability.
Material
Knowing that masks are worn for long periods of time and occasionally in wet/warm environments, mask materials should be innocuous and must adapt to the most sensitive skin types.
Sterility
The third criteria is the sterility or nonsterility of the product. Sterile masks are mainly used in the pharmaceutical sector and sometimes in biotechnology and cosmetics settings. Nonsterile masks are mainly used in industrial sectors such as micro- and nanoelectronics, micromechanics, space and aeronautics, optics, agri-food, and medical devices.
Sterilization Risk Factors
The use of sterile equipment helps to prevent the spread of bacteria or viruses even before entering the cleanroom. However, any type of sterilization involves risk and has an impact on the base material of the product. For masks, the main risk is performance deterioration, although there is the potential for additional impact in the presence of residues which can be toxic to humans. As such, the method of mask sterilization chosen, such as steam sterilization, radiation sterilization (beta/gamma/X-ray etc) or gas sterilization (ethylene oxide) is important. Analysis should indicate a method where performance and control can be maintained and where the levels of residues can be measured and their absence verified.
Risk Control in Sterilization
Risk in product development can be avoided by adopting operation and product qualifications based on strict standards (such as ISO 10993-7 and ISO 14937 used in the sterilization of medical devices). However, a deep-dive risk analysis needs to be performed in parallel to ensure that, after sterilization:
- The cleanroom is protected [a linting test (Helmke test) should to be performed to ensure low particle emissions and that sterilization didn’t alter the mask].
- The user and environment are protected [performance and comfort testing, such as filtration performance and breathability tests (e.g. BFE, PFE, VFE, ΔP) need to be performed without significant scoring changes].
- There is no organoleptic (e.g. smell, color) change [visual and olfactory aspects of the mask need to remain the same].
Regardless of the sterilization method used, it should be well-known, mastered, regulated, controlled, and documented in order to release a product onto the market and available without market saturation.
Sustainability and Sourcing
The final criteria to consider is sourcing and sustainability. The desire by end users for locally produced products is becoming ever more important in order first to avoid supply shortages (as during the Covid-19 crisis) and secondly to meet companies corporate social responsibility (CSR) goals. Such goals are becoming more and more strategically important in the life sciences industry and carbon footprint reduction (via local production) or eco-design in product development (via recycled material components, e.g. mass balance approaches or FSC packaging) are highly encouraged.
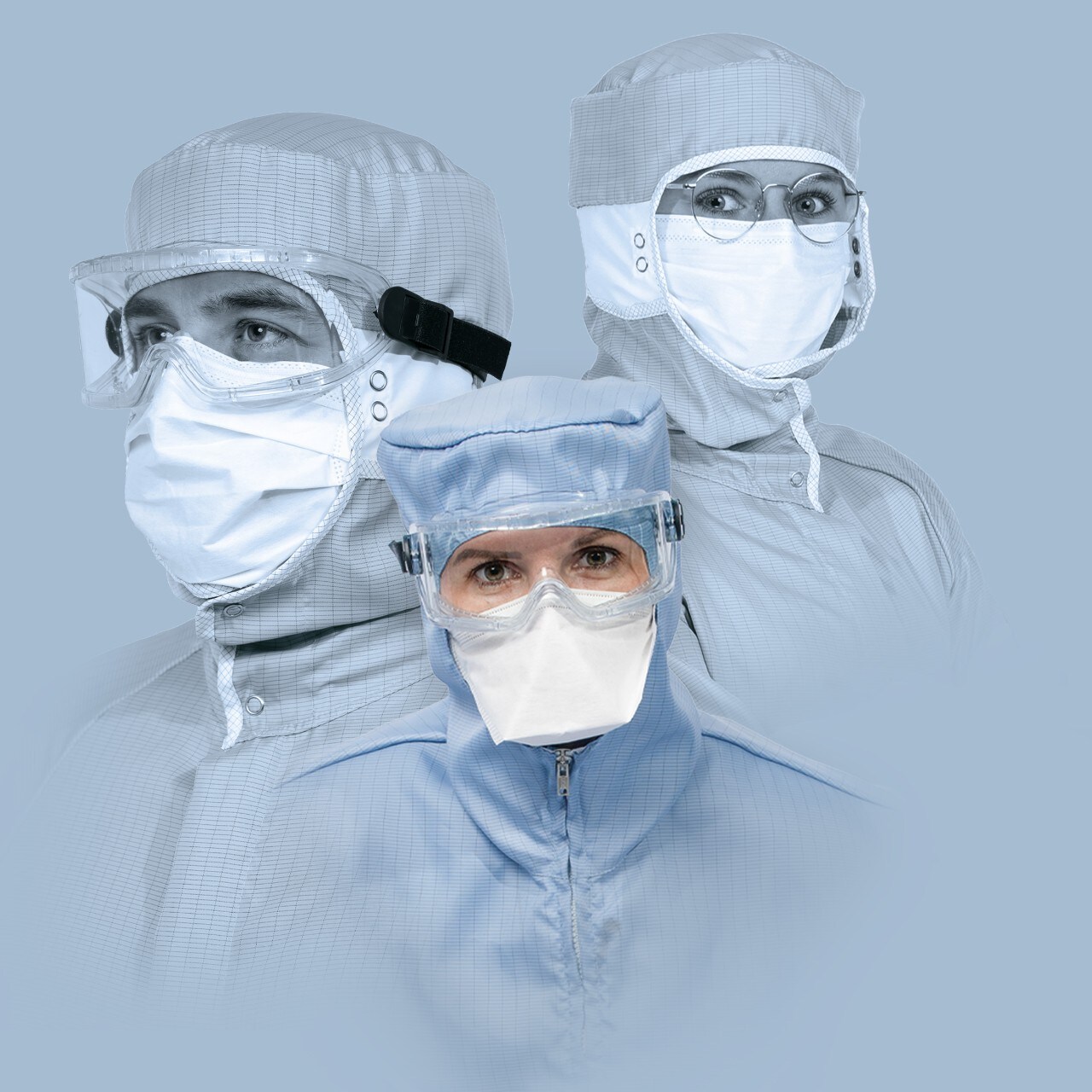
Content provided by:
